A non-destructive approach for assessing the integrity and performance of waterproofing membranes in bridge decks
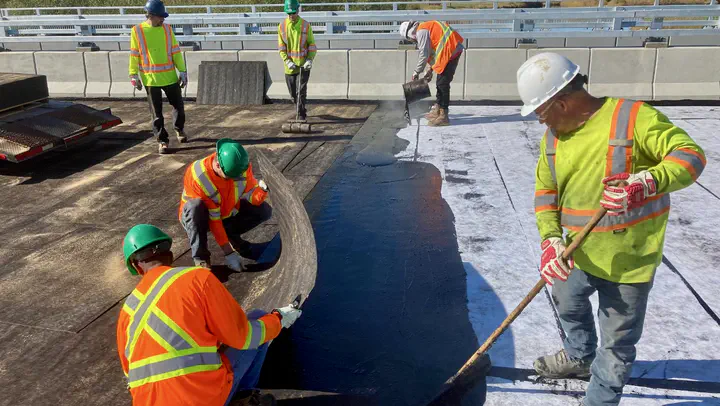
Background Information
A water-proofing membrane under an asphalt overlay is one of the common approaches used for increasing the service life of steel-reinforced concrete bridge decks as the membrane is designed to prevent penetration of water and chloride ions from the road surface to the embedded steel reinforcement below. As such, early detection of the membrane failure before significant chloride penetrates the concrete below represents a low-cost intervention opportunity for bridge deck maintenance.
Chloride salts such as CaCl2, MgCl2 and NaCl are typically used to deice roadways during sub-zero conditions to improve the roadway’s skid resistance. These salts and their ions can penetrate exposed components of a structure such as a bridge deck and initiate chloride-induced corrosion when they reach a critical concentration at the rebar depth. Once corrosion initiates, the corrosion by-products create concrete delamination, spalling and reduction of structural capacity which require costly repairs to complete.
Many approaches have been developed to combat this deterioration process which include the use of corrosion-resistant reinforcement and high-performance concrete designed to limit the ingress of moisture and chlorides. However, these techniques are expensive and create several construction issues that can result in the system being compromised before it is placed into service. An example of this is the use of high-performance concrete typically results in a high-strength concrete that is stiffer than the adjacent element it is attached to. This difference in stiffness results in more frequent cracking which negates the benefit of the high-performance concrete used. As such, many jurisdictions implement a further level of protection by applying waterproofing membranes or sealers overtop of the element to prevent the penetration of water and chloride ions from the road surface and thus prolong the service life.
Many types of waterproofing systems are available such as preformed sheets, hot-applied rubberized membranes, or spray-on liquids. All systems are applied to the concrete surface which is then protected by a wearing surface for elements exposed to wheeled traffic. In Canada, the most common type of membrane used on bridge decks is the hot-applied rubberized asphalt membrane which according to a report from the Transportation Association of Canada (Emery, 2010) has been standard practice in much of Canada since the early 2000s. Similarly, for other elements, the most common type of waterproofing system is a silane sealer.
Currently, there is no known reliable method for determining when an in-service membrane reaches the end of its serviceable life. Hence often these elements are either ignored until significant damage occurs in the deck due to corrosion, or they are replaced even if they are still functioning. Being able to monitor the condition of the membrane to accurately identify defects or when the membrane should be replaced represents an important step in the management of the asset.
The failure of a membrane or sealer is dependent on many factors, such as membrane/sealer type, method of application, traffic load, stiffness of the supporting element, and exposure to abrasion. For bridge decks covered with an asphalt overlay, the membrane performance was found to be highly dependent on the overlay condition (Sohanghpurwala, 2006) as cracking and ravelling of the overlay allows water to access the membrane below which accelerates the deterioration of the membrane.
Premature failure of a membrane/sealer system means a loss of the extra protection afforded by this system from chloride-induced corrosion which can drastically reduce the life of the element. Also, because the membrane failure is often localized, it can produce concentrated corrosion cells that accelerate concrete delamination, pop-outs further deteriorating the element condition. In some extreme cases, pitting corrosion on the embedded reinforcement can reduce the load capacity of the element without visible damage to the deck surface.
Research outcomes
The non-destructive test method developed in this study can be used to assess the quality of a newly installed membrane system or to determine the membrane condition at various points during its service life with the intent of optimizing maintenance interventions.
methods and techniques
To be released after the lift of embargo due to pending patent applications and/or pending publication.